Day in the Life of Ken Seaborne
What’s your name and job title?
Ken Seaborne, National Cage Asset Manager.
What team do you work in at NHS Supply Chain?
I manage the cage team which consists of three people, we are unique as we come from both operations and transport. However, I work within the transport team.
What does your typical working day entail?
A typical day varies according to the needs of the business. Every day starts with formulating data and reporting on the morning Transport Managers call, how many cages are required to complete the days pick and how many will come back in that day on average. Once this is complete, the day starts in earnest. I spend around three days a week at customer premises completing walk around audits and meetings. The other days are spent looking for third parties misuse of roll cages at trusts and at third party premises. The third parties can be laundries, food service companies, sterile waste companies, scrap merchants or hospital auction companies.
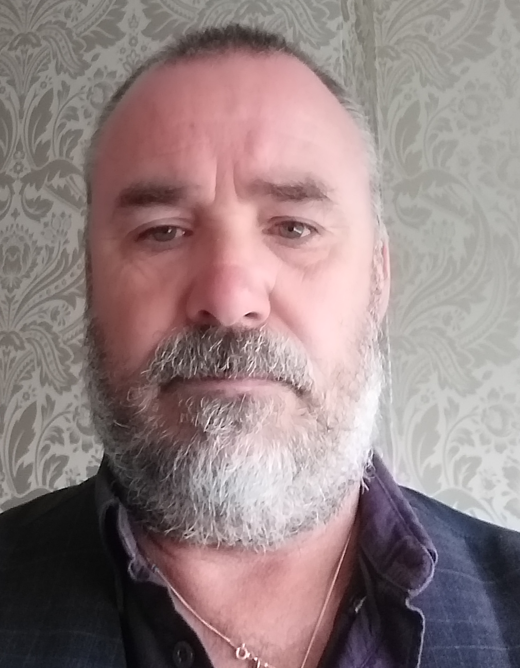
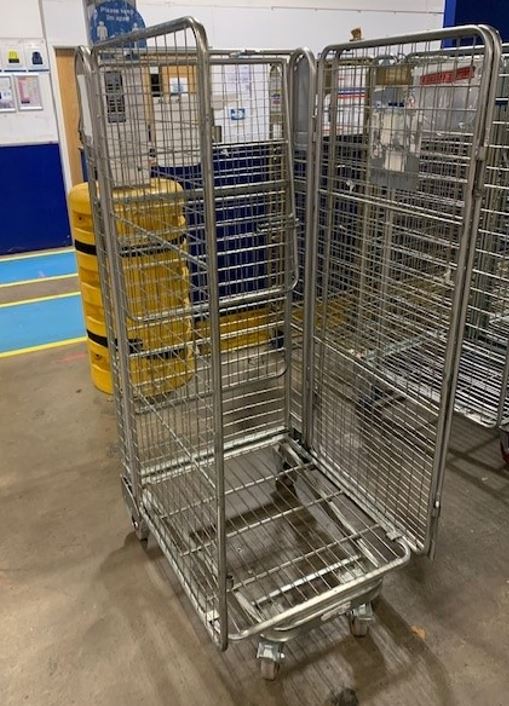
Please can you tell us an example of a successful project you have recently been involved in and what was the value for the customer?
The issue of cage loss has been around for what seems like an eternity. I was tasked to challenge the loss and save on the annual spend of over £1,000,000. I was suggested as a candidate to own the cage repatriation project. I relished the challenge but knew nothing about cages. Luckily for me, there were two subject matter experts within the business (John Hannon at Runcorn and Steve Coop at Normanton). They had been in temporary cage coordinator roles for some time.
The three of us met up and came up with an action plan, this was the start of the journey. In the first year, it was about the loss at trusts and building relationships with customers by offering support, rather than an aggressive approach. We also turned our focus to third-party misuse as part of our plan. We are now four years into the journey and last year we achieved a cost avoidance in excess of £1,000,000. This frees up the money spent on cages to be used elsewhere within the NHS.
We are now four years into the journey and last year we achieved a cost avoidance [on roll cages] in excess of £1,000,000.
What motivates you?
Saving tax-payers money by reducing the need for buying masses of role cages is a big motivator. I also find motivation in challenging third party misuse which we regularly manage.
What job did you to prior to joining NHS Supply Chain? Which previous role did you enjoy the most and why?
I was fortunate to be accepted into the Army at 16. I took a train from Cardiff to Folkestone the day after I left school and my last exam. To be honest, my prospects would have been very different had I not joined.
Finally, tell us about yourself!
I followed a path into transport and military training and never looked back. I left the Army in 2008 after serving in both the regular and reserve regiments and followed the same path in civilian life (except for a stint as a crash investigator for the highways agency on the motorways).
I live with my partner Amy in Tewkesbury. We have six grown up children between us and 13 grandchildren which keeps us busy! We rescue huskies, having two at present, Demon and Sheeba. Demon was his name when we rescued him, but he is a big softy!
They take a lot of exercising, so we spend the weekends walking in the Forest of Dean or the Brecon Beacons.
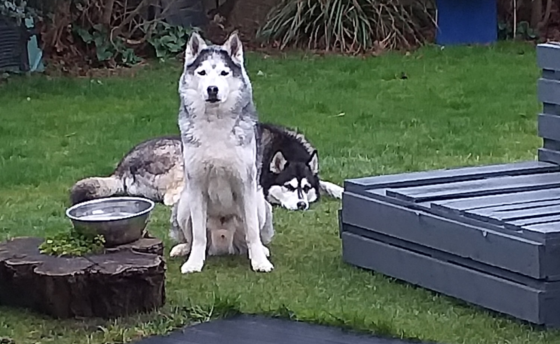
Links section
-
Roll Cage Management
Why effective roll cage management is important to deliver your products efficiently.