Efficient Resource Usage and Waste Reduction on our Medical Pulp Framework – A Blog by Rosy Bennett
I am Rosy Bennett, the newly appointed Sustainability Manager at NHS Supply Chain. Sitting in the wider sustainability team, under the leadership of Heidi Barnard, I will bring passion and drive to further enhance our systems for the benefit of the entire NHS. The chance to influence a substantial portion of the UK’s carbon footprint both excites me and poses a significant challenge.
1Roughly 4% of the UK’s carbon footprint is attributable to the NHS and approximately 62% of the NHS footprint is made up of the goods and services it buys.
Previously I worked for the Nottinghamshire Healthcare NHS Foundation Trust where I was a lead for waste management and environmental compliance. The key focus of the role was waste hierarchy and circular economy principles. Having implemented several waste improvement projects in previous roles I understand the complexity of the task, and I am keen to share improvements within our Medical Pulp framework. Specifically focusing on efficient resource usage, waste reduction and highlighting the value of stakeholder engagement alongside understanding user behaviours within the NHS.
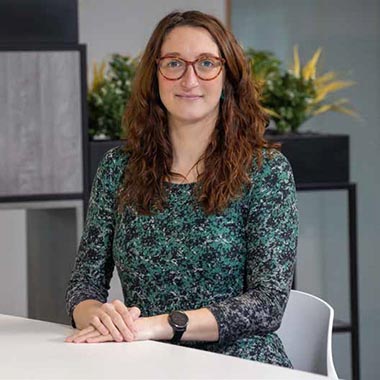
Challenges transitioning to reusable
The 2023 clinical waste strategy by NHS England, along with the revised Health Technical Memorandum (HTM 07-01), emphasises circular economy principles, sustainable procurement, and resource efficiency within the NHS. However, transitioning to reusable products faces challenges due to factors such as:
- Infection prevention and control standards
- The absence of infrastructure to support onsite decontamination
- And staffing pressures.
Engaging with end users of our Medical Pulp framework has provided us with better insight into how these products are used within the care system. This understanding has led to simple actions that will enhance efficiency and reduce waste.
The 4L pulp wash bowls (FSL2144, FSL2230) are single use paper-based items used for cleaning patients at bedsides. Last year over 233,875,800 million of these products were purchased through NHS Supply Chain with a value of £6.8million. NHS Supply Chain has 98% of the market share of sales on these two products.
The survey revealed the practice of ‘double bowling’ where the practice of putting two wash bowls together to attend patient care instead of one is practised. Over half of the clinicians surveyed agreed they were double bowling, when asked the reasoning for this practice, several responses were given including:
- 52% had concerns about the products leaking
- 10% had concerns about loss of dexterity when carrying the product
- 5% were double bowling out of habit.
Additionally, the survey found that the wash bowls weren’t being used for intended purposes, and instead were utilised for emptying catheters or transporting patient property.
If 50% of clinicians stopped practising double bowling to reduce consumption and we also explore other opportunities such as product reengineering, then we could potentially reduce the costs across the system by £1.7 million, this would also equate to a carbon saving of approximately 400 tonnes CO2e. These savings are high level and based on the reduction of the pulp bowls alone and do not include emission from the reduction in packaging, energy consumption for macerators or wider sewerage treatment processes so carbon savings would likely be much higher, however, further work is required to quantify these.
Macerators and environmental impacts
The wash bowls are designed to be macerated after use. Macerators are renowned for breakdowns if not used correctly, which can be disruptive to ward processes and require wash bowls and other items to be diverted to other waste management routes, whilst the macerator is put back into service.
The act of macerating and disposing of waste into the sewer however is not without its environmental impacts. Macerator waste contributes to blocked pipes and sewers which can lead to pollution incidents. The manufacturer’s guidance for the washbowls is that they are macerated individually to reduce the likelihood of breakdowns and blockages. However, this is not common practice.
Feedback from the survey, and the prevalence of ‘double bowling’ prompted the category team to engage with suppliers for additional product testing to determine if there were quality issues. Testing did not identify any concerns with leakage, but it was noted that when the product was filled with warm water and placed onto a worktop condensation appeared on the underside of the bowls. This may potentially be giving the perception that the product leaks. Due to this insight, the manufacturers are exploring reengineering the product to allow airflow to the underside of the bowls for example adding feet to the bowls. Guidance for product use is also being revisited.
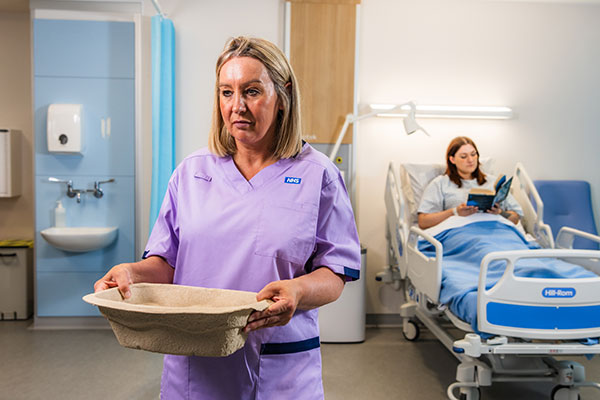
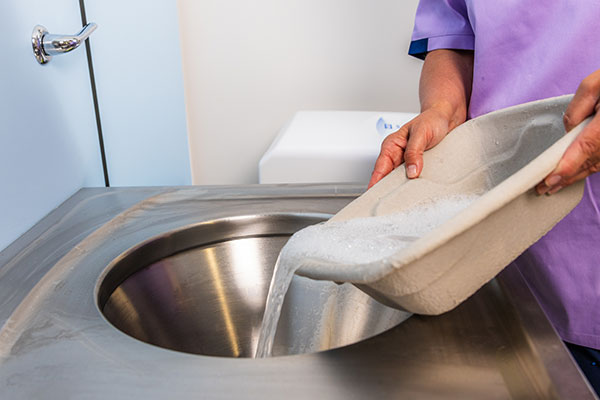
How can your trust take action?
- Contact your procurement team to understand the purchase and usage of these products (FSL2144 and FSL2230).
- Conduct an internal survey to understand product use and staff behaviours.
- Re-educate staff on the issues identified in this blog emphasising the financial and environmental benefits of resource efficiency.
- Monitor consumption of these items pre and post-engagement.
- Develop trust case studies demonstrating savings.
- Encourage staff to identify similar issues and opportunities for resource use and waste reduction.
Next steps
The Medical Pulp Category Team at NHS Supply Chain will keep customers informed as they launch the re-engineered products and update the guidance. Additionally, the Category Team for Medical Holloware is exploring reusable alternatives to single use wash bowls, supporting trusts considering the switch. In some cases, there may also be opportunities to eliminate the use of bowls. In certain situations, it’s worth considering alternatives to using bowls. Clinicians can assess patients individually to see if walking to bathrooms and cleaning facilities is feasible.
Let’s collaborate
The Sustainability Team and Category Team at NHS Supply Chain would like to develop a case study to showcase savings, while also addressing Infection Prevention and Control (IPC) risks and barriers related to the decontamination process. If your trust is interested in exploring this area please contact
Sustainability Team
1 Referenced from Delivering a ‘Net Zero’ National Health Service report.
2 Based on sales figures from April 2023 to March 2024.